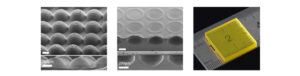
Optimizing Flexible E-Skin Sensors With Micro 3D Printing Technology
The demand for wearable e-skin devices is on the rise, particularly in industries such as biomedical, surgical robotics, and brain-computer interface. These devices are crucial for real-time monitoring of health